We heavily rely on our freezers to keep our drinks chilled and our coolers stocked. So, it's quite bothersome when the ice maker stops producing those perfect little cubes. While you may feel inclined to wave the white flag, understanding why this happens can often lead to simple solutions.
Various factors can halt the ice-making process. Sometimes it's as simple as changing the water filter or adjusting the freezer’s temperature. In other cases, more specific components might be at fault. Recognizing these common issues will help you address the problem effectively, potentially saving you the cost and hassle of having a repair team visit your home.
In this guide, we’ll walk through frequent causes behind ice production woes, helpful tips to solve them, and advice on when to seek professional assistance. Let's dive into the chilly depths of freezer diagnostics to restore your ice-making bliss.
Common Causes
When your freezer won't make ice, it's typically due to a handful of reasons, each with its own telltale signs and effective remedies. Understanding these can be the first step toward a quick solution. One of the most frequent culprits is a clogged water filter. Over time, minerals and other particles in the water supply can build up and block the water line. This prevents water from reaching the ice maker, cutting off its ability to produce ice. If you haven't replaced the filter in a while, this is a great place to start your troubleshooting.
Another common issue is the freezer's temperature setting. Ice makers typically won't function optimally if the freezer's temperature is above 0°F (-18°C). Make sure it's set correctly by consulting your freezer manual. Remember, if the temperature is set too high, the ice won't form, and if it's too low, the unit might freeze over and block the ice ejection process.
The water inlet valve is another key player in the ice-making saga. This valve controls the supply of water into the machine. Sometimes, especially in older units, the valve doesn't open properly due to mineral deposits or mechanical failure. Regular maintenance can often prevent this. Make sure that the water pressure leading to the valve is adequate, using a pressure gauge as needed; a typical fridge requires 20-120 PSI for optimal operation.
According to appliance expert Mark John, "Keeping an eye on the water pressure and regularly cleaning your freezer can significantly extend its life and performance."
Don't forget about the ice maker's control arm. This small plastic lever tells the unit when to cease production once the tray is full. It's possible for the arm to get stuck in the "off" position, either because of ice build-up or because it simply hasn't bounced back correctly. Check this component regularly and make sure it moves freely. This involves simply inspecting the tray and gently moving the arm to see if it's obstructed or jammed.
To round off your assessment, it's wise to consider the water lines as well. Kinks or bends in these hoses can restrict the flow of water. This could happen if the freezer has been moved or tampered with and often needs only a simple realignment to fix. Occasionally, the water line may even freeze. If you suspect this, disconnect it and allow it to thaw completely before reinstalling. Remember, regular defrosting of your freezer can prevent not only the lines but also various components from freezing over.
For tech-savvy users, inspecting the freezer's digital control board or timers can also provide insights. Repairing these requires some expertise, though, as a faulty board might inaccurately regulate temperatures or communicate poorly with the ice maker. Here, professional intervention is typically advised if you've ruled out other issues.
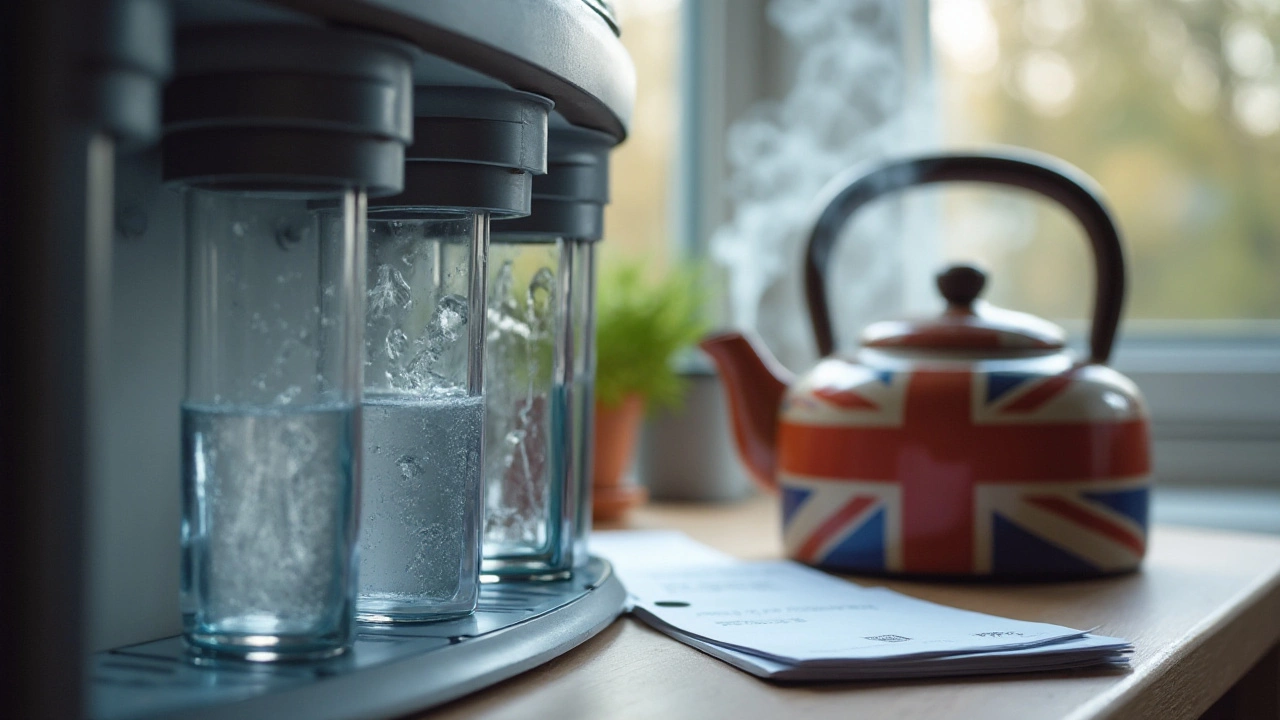
DIY Troubleshooting Tips
If your freezer has stopped making ice, don't immediately panic. Before calling in the pros, there are several DIY troubleshooting tips you can try first. Many of these solutions require just a bit of patience and a screwdriver or two. Remember, the main thing is to stay calm and think through each step.
A great place to start when your ice supply has dwindled to none is to check the freezer's temperature settings. Ice makers typically require the surrounding air to be around zero degrees Fahrenheit to function optimally. If the temperature is too high or too low, it can affect how quickly ice is produced — or if it's produced at all. Grab a reliable thermometer and place it in the freezer overnight to verify exact temperatures. Reports from appliance experts suggest that this minor adjustment could solve the issue in nearly 50% of cases.
Next, consider examining the water supply line to the ice maker. Although often overlooked, if there's a kink or clog, the water may not be reaching the unit. With the freezer unplugged, trace the supply line for any visible blockages or bends. If you spot one, gently iron out the kinks to allow smoother water flow. Don’t hesitate here — this simple fix can magically restore your ice-making capabilities!
Additionally, take this opportunity to inspect and replace the water filter. A clogged filter can severely impact water flow to the ice maker. Filters should be replaced every six months to ensure they function properly. You'd be surprised to learn from appliance industry surveys that a vast number of households forget this critical maintenance step. If your water filter light is on, or you can't remember the last time you replaced it, swap it out. Brands usually provide straightforward instructions or try following this generic procedure: twist out the old filter, insert the new one until you hear a click, and voilà, you're done!
On occasion, more peculiar glitches might interrupt ice making, like the ice maker cycle that has stalled midway. Peel back the freezer's front panel to access the ice maker control. Press the reset button for a thorough reboot, or manually adjust the arm to kickstart the cycle again. While it might seem unnecessary, small reboots just like this can revive electronics and mechanical parts alike.
In the words of Tony Locker, a reliability technician, "Your appliance is more forgiving than it's perceived. Try the small fixes first because they're often your golden ticket to resolve sticky situations."
A simple step that some folks overlook is to ensure that the ice maker's switch is flipped to the 'on' position. Check this before any other troubleshooting step—if it’s accidentally switched off, no amount of cleaning or maintenance will encourage the hardware to make ice cubes. Be sure to give it a nudge back on.
Tackling some of these troubleshooting tips can often save you the time and expense of a professional repair service. These are not difficult tasks and can often be performed with tools you have lying around the house. Remember to plug the appliance back in once you've conducted your checks. And voilà, with any luck, you're back to hosting icy-cold drinks at your next party in no time!
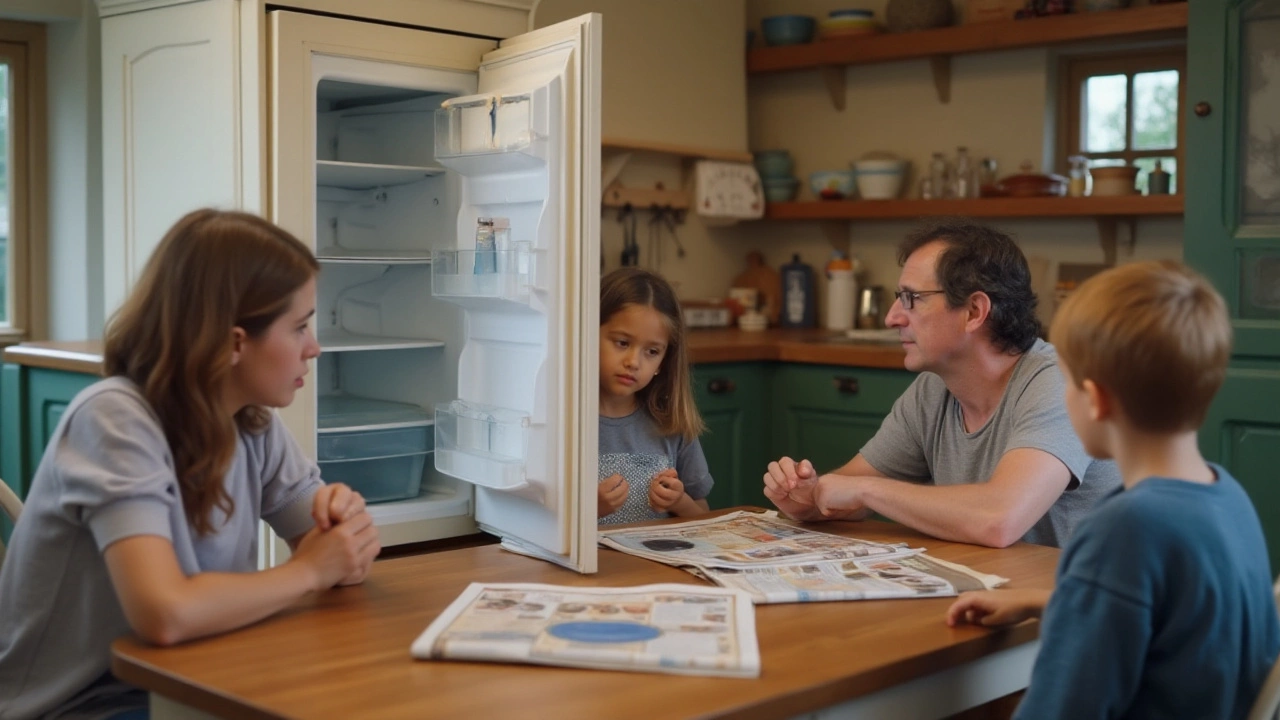
When To Call A Professional
Just as there are times to take on repairs yourself, freezer repair situations often arise where calling a pro is your best bet. While minor issues like a clogged water filter or a misaligned ice bin are great DIY projects, certain problems require professional expertise. These experts bring a wealth of experience and knowledge, saving you the frustration of trial and error and ensuring the job is done right. An ice maker that fails repeatedly despite your best efforts can indicate a complex underlying issue—something only trained eyes can identify.
For instance, if your freezer's ice maker is leaking water or forming unusual ice shapes, it might not just be a nuisance; it could signal a deeper mechanical problem. This could mean anything from damaged fill tubes to faulty solenoid valves. Not only do these components need proper handling, but they also often require specific tools to service or replace them efficiently. Attempting these repairs without the necessary expertise might not only worsen the situation but can also void any warranty your appliance might have.
There are also indications of electrical or digital problems that demand a technician's proficiency. Modern ice makers can feature intricate digital systems that may need diagnostic tools to understand. If the unit shows error codes or the control board isn't responsive, trusting an expert with relevant equipment is crucial. Continuing to fiddle with these parts when unsure might lead to more harm than good, possibly causing irreversible damage or introducing safety hazards.
"A technician can quickly pinpoint issues that might take the untrained eye ages to detect," says Jake Morrison, a seasoned appliance repair specialist. "It's often cheaper in the long run to get professional help, rather than risk further problems down the line."
Moreover, ice maker problems might be rooted in freezer-wide issues such as refrigerant leaks or compressor failures. These are not only complex but also carry environmental considerations, necessitating proper credentials to handle and dispose of chemicals safely. If your machine is producing too little or too much ice constantly, it might be intertwined with such systemic problems beyond the reach of basic troubleshooting.
If you're considering repair costs, it's key to balance this against the expenses of a full replacement. A credible technician can provide insights into whether your appliance is worth fixing or if upgrading to newer models might be more cost-effective. Attempting repairs without the proper expertise can end up being a costly endeavor. So, whenever in doubt, remember that the guidance of a professional can provide peace of mind, preserving both your freezer's functionality and your domestic tranquility.
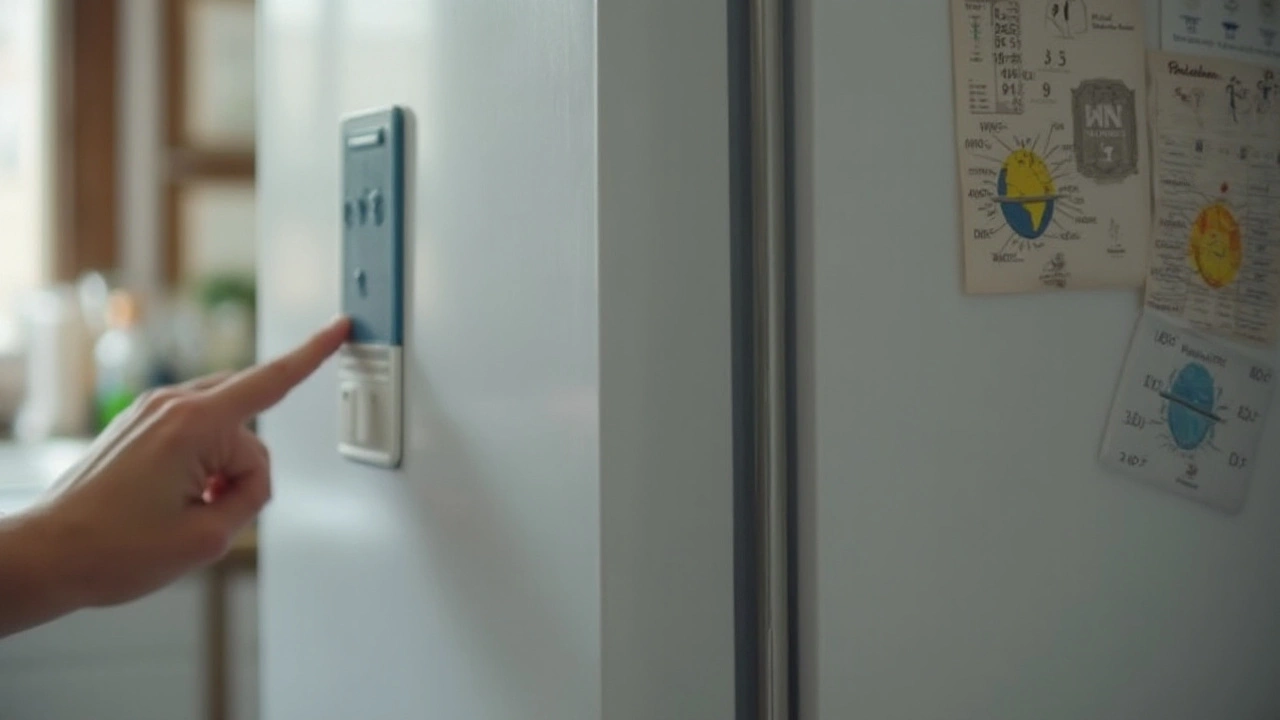
Preventative Maintenance
Preventative maintenance for your ice maker isn’t just a good idea—it’s essential for keeping it running smoothly and efficiently. One of the most important steps is to regularly replace the water filter. This simple action can prevent clogging and ensure that your ice remains fresh and pure. A clogged filter can block the flow of water, a common reason why your ice maker might stop working. Keeping a schedule for changing your filter every six months is a reliable guideline to follow.
Another vital practice is cleaning your freezer regularly. Ice makers can harbor mold and mildew, especially around the chute and ice bin. Removing the ice bin and cleaning it with warm, soapy water can prevent these issues and keep your ice tasting clean. Also, make it a habit to inspect the freeze unit for any stuck cubes, which can affect the mechanism and cause blockages.
"Regular maintenance is the key to keeping household appliances in top shape, reducing unexpected breakdowns, and extending their lifespan," says household appliance expert Maria Black.
If you're concerned about energy usage, make sure the freezer is not overloaded. Overcrowding can upset the airflow, which ensures that all sections receive uniform cold air. This can lead to uneven freezing and affect ice production. Allow for a couple of inches of space around the internal walls for optimal air circulation.
Using these preventative measures can also highlight potential issues before they become major problems. Regularly check for noises or leaks around the ice maker. Strange sounds may indicate a malfunctioning part. While leaks might suggest problems with the water line connection. If detected early, these can be repaired with minimal cost and inconvenience.
Finally, consider investing in a water softener if you notice hard ice or mineral deposits. These deposits can damage internal parts, causing the ice production to slow down. With a bit of diligence and routine attention, your freezer and ice maker will run efficiently, ensuring you never run out of ice when you need it most.
Task | Frequency | Purpose |
---|---|---|
Replace Water Filter | Every 6 Months | Prevent clogging, ensure fresh ice |
Clean Ice Bin | Monthly | Prevent mold and mildew |
Inspect Freezer | Monthly | Check for noises, leaks, or malfunctions |
Avoid Overloading | Ongoing | Ensure proper airflow and freezing |
I am an expert in the services industry with a focus on appliance repair. My passion lies in understanding how things work and educating others in simple, engaging ways. This enthusiasm fuels my writing, where I delve into topics around appliance maintenance and troubleshooting. I aim to make these subjects clear and accessible to all readers.